Three recent case studies reaffirmed Gaylin International Pte Ltd and Rigmarine’s (part of its group of companies) statuses as pioneers in the wire rope and spooling sector.
Put simply, spooling is the activity of winding onto a spool, but when offshore and marine applications are concerned, staggering dimensions and other factors put it among the most specialised and challenging fields of expertise.
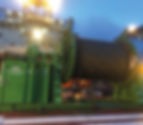
Mike Duncan, Managing Director at Gaylin, said:
“As it pertains to our work, it [spooling] is basically about the handling of long lengths of wire rope, typically in the marine and / or lifting industries. Anchor wires, A&R [abandon and recover] wires, mooring systems and crane ropes all present their own spooling challenges and few companies excel at this activity.”
Three projects prove the point. Two case studies presented a simultaneous challenge to install A&R wire rope packages aboard vessels in Malaysia and Azerbaijan respectively. One docked at Johor Port required 109mm x 3,000m, 160t capacity rope. In Baku, aboard another, 112mm x 3,000m rope of 155t capacity was the order of the day.
Duncan reflected on the scale of both projects, recalling local mobilisation of engineers and machinery from Gaylin’s offshore marine base in Johor and Rigmarine’s Azerbaijan facility. Each location provided an engineering team of at least 12 people, including project management as well as two spooling machines of over 200t capacity. He said: “Due to irregular reel dimensions in the Caspian, re-engineering of the 200t spooling machine was required in a short timeframe to avoid mobilisation of a specific machine from Europe. This saved the client in excess of $50k alone.”
A winch test system was provided to the same project with specific components, such as a 500t triplate, 500t wide body load measuring shackles and synthetic grommets. Both projects were completed within budget, on time and without incident, Duncan added.
The scope of work for the third job, meanwhile, was to provide engineering and methodology for changing out the main hoist ropes of a unique 2,400t capacity ‘sky hook’ crane, including a solution for removal of the 15-degree twist apparent on the hook block.
A team, mobilised from Gaylin China, comprised a project manager / HSE representative, mechanical fitter, machine operator and four qualified wire rope technicians. From the same facility, a 65t back tension spooling machine was provided alongside a support loft containing all required rigging and consumables. The project was completed ahead of schedule, allowing the crane to return to productivity, saving on downtime and directly contributing to the customer’s bottom line.
Duncan concluded: “As a group we have the largest fleet of spooling machines with in excess of 30 units. However, it’s one thing having the equipment, but another ensuring one has the experience and competency to provide world-class solutions.
Many wrongly believe it’s all about investing in the kit and forget about the ability to safely use it. All of our equipment is in line with controlled European and international standards such as LOLER and PUWER, and all of our technicians go through tailored and rigorous training courses.”